Oerlikon Focusing On Creating Circular Economy At ITMA
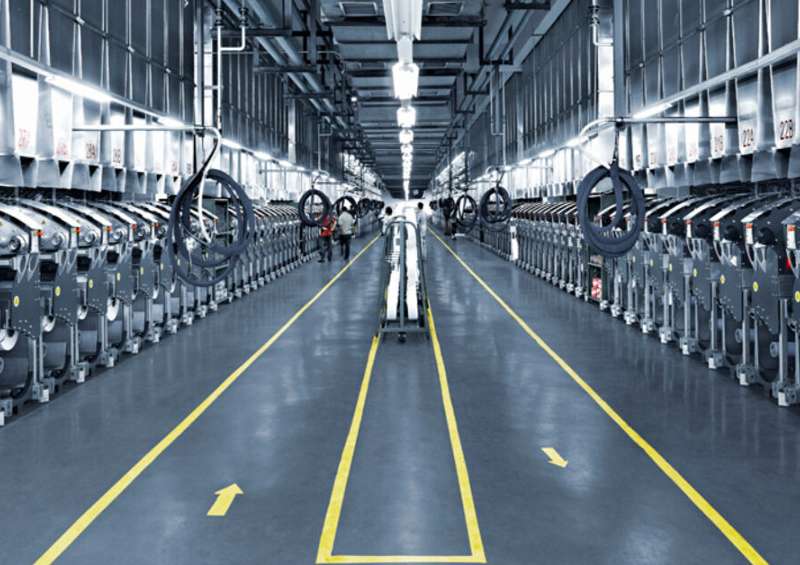
Germany based Oerlikon Group will focus on creating a circular economy within the textile value chain, which is among the various and current challenges that the entire textile industry is facing at ITMA in Hall 1, Stall B211.
Oerlikon Group will also focus on other challenges like providing energy-efficient technologies, using digital solutions to support a sustainable production, processing new materials, and finally the traceability of all products and the recycling of raw materials used.
In order to create a circular economy, Oerlikon is intensively involved in Worn Again Technologies, which focuses on a solvent-based recycling technology, with which both end-of-life textiles comprising polyester and poly-cotton blends and PET plastics can be converted into circular raw materials and fibres.
Oerlikon Barmag is also offering technological solutions for rPET that enable customers to save million tons of CO2 per year.
Also on display is a homogenizer recycling line, where bottle flakes and film waste can be agglomerated, extruded, homogenised and melted to produce polymer melt or chips.
It enables the polymer quality of recycled bottles or film waste to be precisely adjusted to the requirements of different downstream extrusion or injection molding processes.
Another rPET solution is the VacuFil system which is a unique and innovative PET recycling line, uniting gentle large-scale filtration and targeted intrinsic viscoscity (IV) regulation for consistently outstanding rPET melt quality.
Oerlikon Neumag will be unveiling its new EvoSteam process, which according to the company is an enabler for more sustainable staple fibre production in the future.
The objective of the new development is to lower both operating expenses and the carbon footprint with minimal consumption of energy, water and polymer, simultaneously with the excellent fibre qualities demanded by downstream processes and high production volumes.
At the show, Oerlikon will also present its own digital technology solutions and those that have been tested in collaboration with various partners for the use in Oerlikon technologies.
Oerlikon Barmag will also present a complete WINGS POY winding head as a kinematic model as a digital twin. For this purpose, all essential machine components were modeled as rigid bodies and connected to each other via joints and contact bodies.
The actuators present in the real world were simulated by forces and moments. Analogously, the sensors are simulated by contact bodies and corresponding collision bodies.
With this kinematic model, it is now possible to map all the processes that occur during the operation of a winding head in virtual space. Customers can thus be offered faster and more cost-effective production solutions.
Also on show is the upgrade of ACW WINGS drawing fields, in which, on demand from its customers, the company has integrated a WINGS drawing field in combination with virtual ACW Winder.
The new JeTex is a production line for high-quality air-textured yarn (ATY). It combines an innovative texturing system developed as a key component with components by Oerlikon Barmag to ensure fast production speed, the desired effects, and the quality of the product.