Shimmy Technologies Trains 10,000th Worker, Unveils New Expansion Plans
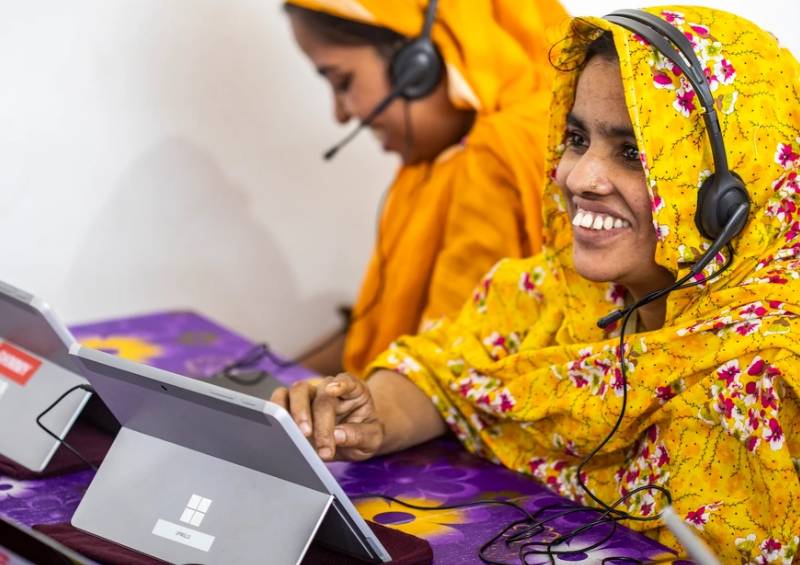
Shimmy Technologies, a leader in industrial education technology, proudly announces a significant milestone: the successful training of its 10,000th worker.
Leveraging a cutting-edge blended learning model, Shimmy combines gamification, AI, and traditional machine training to reimagine workforce development. This approach optimizes training costs and time, meeting the demands of today’s economic landscape and complex supply chains.
“This milestone underscores our team’s unwavering dedication and commitment to delivering top-notch training while efficiently scaling our operations,” remarked Sarah Krasley, CEO at Shimmy Technologies. “Our recent investments in the Shimmy platform empower us to reach more workers without compromising the quality of our training.”
Shimmy’s innovative approach yields remarkable results. A majority of trainees secure higher-level positions and command better starting salaries, with over 50% advancing to more complex machine roles within their factories. Notably, 72% of those receiving advanced manufacturing training identify as women, marking a significant stride towards gender equity in the industry.
An independent efficiency study recently validated Shimmy’s training methodology. The study highlights substantial improvements in factory efficiency, reduced absenteeism, and increased worker motivation, proving the commercial value of Shimmy’s training.
Looking forward, Shimmy Technologies unveils plans for forthcoming developments aimed at accelerating speed, scale, and outreach. These initiatives aim to support workers in new ways and fortify supply chains amidst extreme volatility.
“In the coming months, we’ll be rolling out new features that will enable us to reach even more workers, faster and more efficiently,” added Krasley. “We remain steadfast in our mission to empower workers with essential skills, helping them justly transition if displaced, and stay relevant as employers look to new ways to build resilience in their production lines.”
According to Shimmy’s research, the number of automated machines in participating factories will increase by 13% over the next two years. Factories anticipate that each machine could displace between 1-6 workers per machine. This displacement is expected to disproportionately impact female workers, as only 20% of factories expressed a preference to address the gender gap and promote female workers to operate the automated machines.