Chalk-Based Coating Creates Cooling Fabric
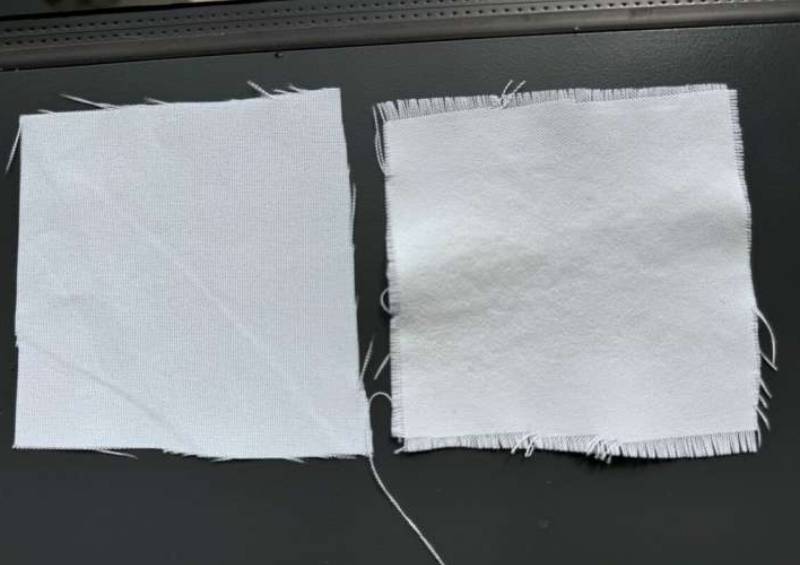
A new chalk-based coating has been developed to create cooling fabrics that could benefit anyone spending time outdoors—athletes, landscapers, kids at the park or beachgoers. While current cooling textiles often rely on specialized fibres or complex manufacturing processes, researchers have now introduced a durable coating that cools the air underneath treated fabric by up to 8 degrees Fahrenheit.
Evan D. Patamia, a graduate student at the University of Massachusetts Amherst, will present the team’s findings at the American Chemical Society (ACS) Fall 2024 meeting. The event, held both virtually and in person from August 18-22, features around 10,000 presentations on various science topics.
According to Trisha L. Andrew, a chemist and materials scientist working with Patamia, “When you step into sunlight, both your body and clothing absorb UV and near-infrared (near-IR) light, which increases heat.” The goal of recent innovations in textiles has been to develop materials that not only deflect the sun’s rays but also push out natural body heat—a process known as radiative cooling.
Existing solutions often use light-refracting synthetic particles like titanium dioxide or aluminum oxide, or organic polymers that require PFAS chemicals, which pose environmental concerns. Andrew’s team sought to create a more sustainable alternative using natural materials. They leveraged their experience with chemical vapour deposition (CVD), a method that combines synthesis and coating in a single step, to apply a durable polymer layer on fabric.
Inspired by historical limestone-based plasters used to keep houses cool, Patamia and Megan K. Yee developed a process to incorporate calcium carbonate (the main component in limestone and chalk) and bio-compatible barium sulfate onto the polymer layer. Calcium carbonate reflects visible and near-IR wavelengths, while barium sulfate reflects UV light.
The researchers applied a 5 micrometer thick poly (2-hydroxyethyl acrylate) layer to fabric squares and dipped them in solutions containing calcium or barium ions and carbonate or sulfate ions. The process, which involved multiple dipping cycles, resulted in a chalky, matte finish on the fabric. By adjusting the number of cycles, the team optimized the particle size distribution for effective light reflection.
Outdoor tests showed that the treated fabric created air temperatures up to 8 degrees Fahrenheit cooler than the ambient temperature in direct sunlight, with a maximum difference of 15 degrees Fahrenheit compared to untreated fabric, which actually increased air temperature underneath.
Patamia remarks, “We see a true cooling effect. What’s underneath the sample feels colder than standing in the shade.” The coating also withstood laundering tests, retaining its cooling properties despite friction and detergent exposure.
Andrew, who is involved in a startup scaling the CVD process for larger fabric bolts, envisions translating these innovations into pilot-scale production. She concludes, “Our technique can be applied to nearly any commercially available fabric to create a cooling effect without power input, providing a valuable solution for people in extremely hot environments.”