Digital Printing Emerges As Eco-Friendly Champion In Textile Industry
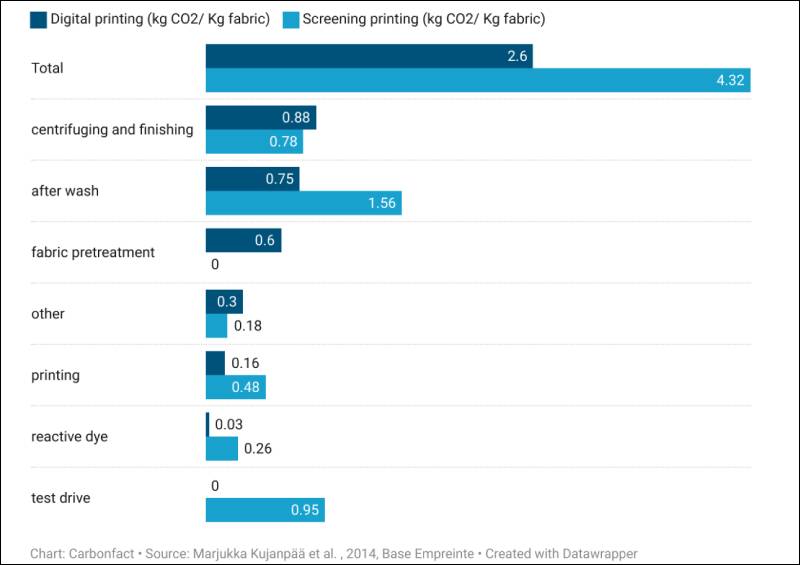
Textile production is a significant contributor to water pollution, with dyeing and finishing processes accounting for approximately 20% of global freshwater contamination. Fashion brands are now exploring alternative colouring methods like screen printing, digital printing and fabric dyeing to mitigate environmental impact. While digital printing has advantages in water and chemical usage over traditional dyeing methods, it does have its own environmental drawbacks, such as the carbon footprint associated with electricity consumption.
Overview of Techniques:
- Screen Printing: Screen printing is a traditional method involving ink forced through a stenciled screen onto fabric, suitable for small to medium production runs. The process includes mixing reactive dye and printing paste, test prints for quality assurance and post-printing steps like washing and finishing.
- Digital Printing: A more recent method using inkjet technology to apply ink directly onto fabric, digital printing offers quick, high-resolution designs. Unlike screen printing, it allows multi-colour designs without multiple screens. Disadvantages include colour bleeding, higher ink costs and reduced washability.
- Fabric Dyeing: Fabric dyeing involves immersing fabric in a dye solution to colour the entire material, often used for solid-coloured fabrics. Traditional methods use synthetic or natural dyes, and the process includes dye immersion, squeezing through rollers to remove excess dye liquor and post-dyeing treatments.
Defining Boundaries of Process Analysis
For accurate carbon footprint assessment, clear boundaries are established for each process, outlining specific steps involved. This ensures consistent and accurate evaluation of energy and material consumption for producing 1 kg of printed or dyed fabric.
Carbon Footprint Analysis
Using a scientific paper as a baseline, the carbon footprint for 1 kg of fabric (GSM 200) was assessed for screen printing, digital printing and fabric dyeing in Europe. The base case scenario results indicated that digital printing has a significantly lower carbon footprint compared to screen printing.
Screen Printing vs Digital Printing
Screen printing’s higher energy consumption in test prints and after-wash phases contributes to a greater carbon footprint compared to digital printing. Digital printing generates approximately 2 kg CO2e per kg of fabric less than screen printing, making it the less carbon-intensive choice.
Digital Printing vs. Fabric Dyeing
Comparisons with fabric dyeing revealed that digital printing can reduce carbon emissions by approximately 1 kg CO2e per kg of fabric. The heat-intensive nature of dyeing processes contributes to this difference.
Energy Source Consideration
The source of energy significantly impacts the carbon footprint of the dyeing process. In regions where coal or natural gas are common heat sources, fabric dyeing may be preferred. Switching to low-carbon heat fuel methods, like biofuel or solar thermal water heating, can contribute to decarbonizing the dyeing process.
Conclusion
In choosing between screen printing, digital printing and fabric dyeing, digital printing emerges as the environmentally preferable option, offering lower water usage and reduced carbon footprint. Consideration of energy sources becomes crucial in determining the overall sustainability of each method, emphasizing the importance of transitioning to more sustainable energy options in textile production.