Indo Texnology’s ‘Auto Cone Pack’ System A True Trailblazer
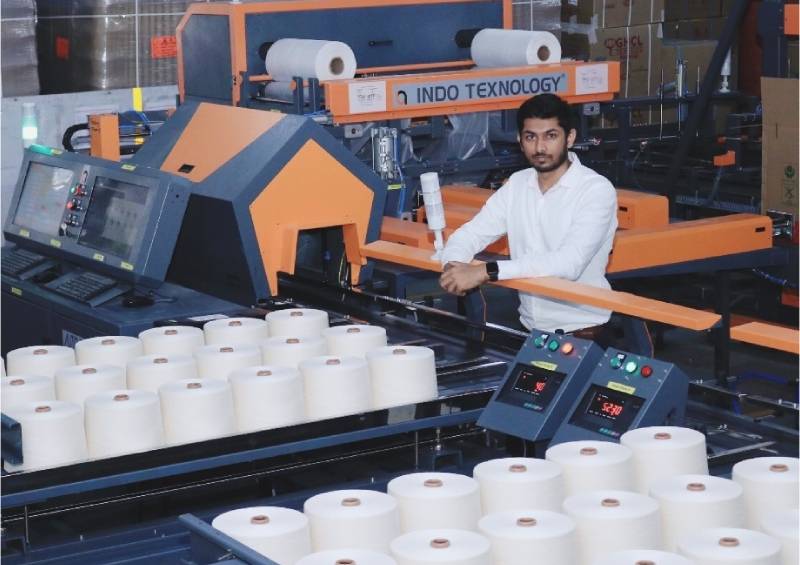
Indo Texnology, a forerunner in conceiving and delivering innovative solutions for textile mills, has become a pioneer in automatic cone packing and cone inspection using camera vision – artificial intelligence.
The Auto Cone Pack System takes care of cone weighing, cone inspection, polythene wrapping for individual cones, and packing into the required formats i.e., bags, boxes, and pallets.
Furthermore, barcode or QR code labels are generated and struck on the finished packing which can be integrated to the inventory management system and all the packing data is integrated into the ERP/Mill Information System.
Indo Texnology was founded in 2007 by Mr Thirupathi, who has almost four decades of experience in the textile industry and has traveled widely across most textile hubs in the world. He foresees pain points faced by spinners, and continuously has a vision to develop innovative and appropriate problem solving solutions.
“Indo Texnology through its journey has been fueled by a passion for innovation and a customer-centric approach. With cutting-edge solutions and unwavering commitment to excellence, the company has redefined industry standards and is shaping the future of textile manufacturing,” Jaivardhan T, Director at Indo Texnology told Textile Insights.
The Coimbatore based company’s first innovation was the Automatic Balepress, the BaleXPRESS, which too is a first in India. Back then and even now, manual presses are a huge concern of safety for operators and mills were prone to a substantial number of accidents, which is the main reason for the success of the BaleXPRESS.
The next innovation was Sortlink – Bobbin Colour Sorting System followed by its upgraded version, the Sortlink Magic – using camera and artificial intelligence to sort bobbins.
The Sortlink is attached to magazine type autowinders and segregates empty bobbins colour-wise. The full bobbins which are rejected from the auto winder and the remnant yarn bobbins are also segregated. Sortlink Magic uses a camera plus artificial intelligence to provide 100 percent accuracy in sorting.
The Sortlink Magic was designed and developed by Indo Texnology after collecting feedback from its existing users. And hence, the Sortlink Magic does not require any additional space to sort the bobbins, can sort bobbins of close shades which is very useful for melange yarn producers, no skill required to operate the machine, and requires close to zero maintenance.
The Sortlink Magic also generates data reports of ejections, which mill managers can use to monitor the autowinders’ efficiency,” Jaivardhan explained.
Next, the company’s innovation was the Cone i, again a camera vision based cone inspection system. The Cone i is integrated with the Auto Cone Pack System and monitors cone tip design to avoid count mix-ups while packing. It also monitors UV defects or UV contamination or Rings as well as stitches defects.
The cone i – Camera Vision Based Cone Inspection System which is placed on the automatic cone packing system adds huge value to the spinning mills by ensuring count mix-ups in packing don’t happen, and preventing defective cones from being packed.
“The Cone i is also capable of recognising other types of defects and is open to a few customisations based on our customer’s product applications and requirements,” he stated.
Another innovation was the Cone Transport System (CTS), which picks up cones from the autoconer, transfers them to the packing area, and sorts the cones, count-wise. The cones are then packed using the Auto Cone Pack System. A yarn conditioning plant can also be integrated into the process.
“With our continuous efforts in development of our solutions, we are the market leaders in the solutions that we provide. With these technologies, we have also built a global presence and are competing with European brands,” Jaivardhan informed.
Indo Texnology puts itself in the shoes of its customers, identifies their pain points, conceives a solution, and designs to the context. This makes its products compatible with regards to operator usability, while providing low recurring costs.
“Our endeavour is to implement advanced technologies in our products across all dimensions, whether software, electrical or mechanical. We never compromise on the quality of components used in our products. This has ensured customer satisfaction and repeat orders,” Jaivardhan stated with pride.
When it comes to after sales service, all their products and solutions are IoT based and so, any troubleshooting can be done remotely, by just connecting with its support team. The company also has a dedicated team of field engineers for support across India and in some international locations too.
The company has a dedicated R&D facility recognised by the government, and this facility is at the core of all the technological innovations, while also constantly updating the existing product range.
Using its technological prowess in camera vision and artificial intelligence, the company has recently launched the Knit i, an online inspection system for knitting machines.
The Knit i is fixed on the circular knitting machine and detects fabric defects during production of knitted fabrics. Indo Texnology has expanded its horizons with Knit i, which enhances quality control in real-time.
“One of the key factors contributing to our success is the perfect synergy between our deep field knowledge and our expertise in technology. Mr. Thirupathi’s foresight and understanding of spinning requirements, combined with Harshavardhan Thirupathi’s mechanical design and artificial intelligence prowess, have been instrumental in our achievements,” he concluded by saying.