Quicksilver Seamlessly Moves From Screen To Inkjet With Mimaki
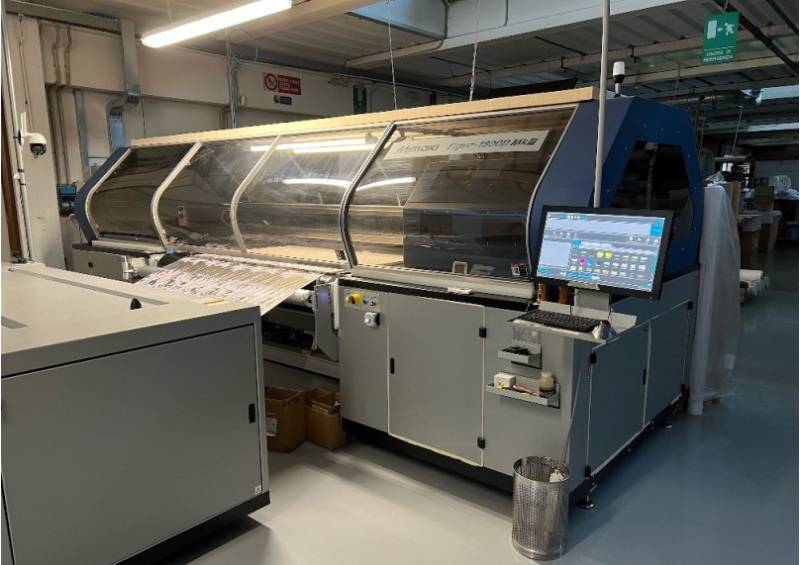
Italian company Quicksilver seamlessly moved from screen print transfer to inkjet transfer printing thanks to the extensive range of Mimaki technologies on offer.
Quicksilver recently invested in a Mimaki Tiger-1800B MkIII unit to efficiently increase the production volumes, while ensuring the high-quality standards the company is known for are met.
Specialised in manufacturing digital printed fabrics and garments for various textile segments, Quicksilver has leveraged cutting-edge sublimation printing solutions to diversify and strengthen its production.
The Mimaki Tiger-1800B MkIII is a cutting-edge industrial printer that offers higher speeds, higher productivity, and unmatched quality.
The Tiger-1800B MkIII features Mimaki’s advanced print technology offers stunning print quality for both direct and transfer printing.
Quicksilver invested in its first Mimaki inkjet sublimation printers in 1997. Since then, Quicksilver has kept a keen focus on inkjet sublimation printing and continues to make further investments in Mimaki technologies.
The Italian company discontinued screen printing about five years ago and now focuses on inkjet printing exclusively.
Quicksilver has now consolidated its position as a leading supplier in sportswear, fashion, high-end fashion accessories market segments, as well as in the gaming and soft signage space.
Its product portfolio ranges from technical sports clothing, printed apparels and garments, printed fabrics for luxury accessories like umbrellas, printed fabrics for gaming tables and soft signage applications.
Besides a diverse product portfolio, the company also offers all-round services ranging from ‘print and transfer’, the supply of sublimation printed paper rolls and the transfer process only.
“The Tiger-1800B MkIII proved extremely cost-effective and efficient. It has allowed us to produce higher industrial volumes and completely transformed our business,” Quicksilver founder Plinio Cecchin said.
“We estimate that we have been able to cut the energy cost due to increased production efficiency,” he added.
“Additionally, using 10-liter ink tanks has generated savings of up to 25 percent on the costs of the inks, and likewise the jumbo rolls which are extremely efficient to load and unload,” Cecchin stated.