Revolutionizing PET Recycling: From Bottles To Fine Filament Movement
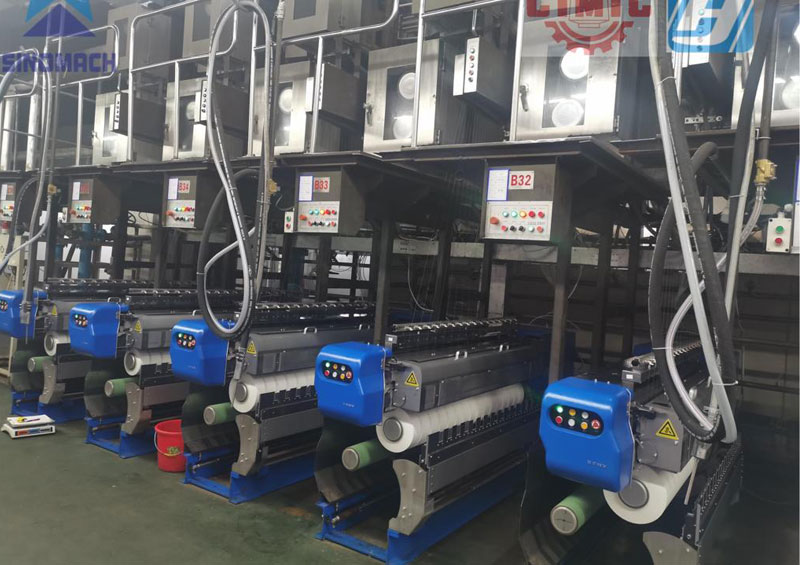
In the current scenario, PET bottle flakes are being extensively converted into fiber in India. The journey began with a capacity of 20 TPD approx. and has now escalated to a range of 80 to 100 TPD for solid fiber production. Numerous cotton/polyester spinning companies are now taking the initiative to establish polyester recycling fiber plants with capacities ranging from 80 to 100 TPD, primarily for their own consumption. Simultaneously, certain companies have opted for smaller capacities, around 30-50 TPD, focusing on hollow or color fibers. It is worth noting that Chinese production lines are favored over European brands.
While expanding within the fiber industry, some companies have recognized the potential of RPOY/RFDY (Recycled Partially Oriented Yarn/Recycled Fully Drawn Yarn) and have invested in new technologies, such as finisher systems in mechanical recycling processes. RPOY/RFDY production is particularly promising area of development. However, this demands high-quality PET bottles, especially when compared to the requirements for Recycled Polyester Staple Fibre (RPSF). The challenge lies in utilizing color PET bottles and color polyester yarn and/or fabric waste to create low Denier per Filament (dpf) and RPOY/RFDY with a dyeing guarantee. To address this challenge, there is a patented chemical recycling process available that extends up to the monomer stage, ensuring color removal and the production of fine dpf RPOY/RFDY with dyeing guarantees. While this approach involves substantial capital investment, it holds significant potential. Selecting appropriate equipment from Pet flakes preparation to winders for RPOY/RFDY lines is crucial. Opting for Chinese machinery complemented by key European equipment appears to strike a balance between investment costs and quality considerations. Maintaining consistent melt control and implementing fine filtration are vital to achieve fine denier and low dpf recycled products and control pressure fluctuations.
In instances of physical recycling, the preparation and drying of raw materials play a pivotal role, particularly when downstream degassing extruders are not available to mitigate damage to the polyester melt. Homogenization is also critical for specific raw materials, aiding in increasing and maintaining the required Intrinsic Viscosity (IV) as per process demands. It is essential to transmit this consistent IV to the spin beam, especially when aiming to produce fine dpf RPOY and operate at higher speeds on DTY machines. Overcoming these challenges will undoubtedly lead to the creation of improved RPOY.
Furthermore, the bottle-to-bottle recycling concept is gaining traction. Companies that recycle PET bottles into fibre are now considering bottle-to-bottle (B-to-B) plants with regulatory compliance in mind. To meet FDA and EFSA compliance standards, companies intend to use the best quality PET bottle flakes for their B-to-B recycling projects to ensure high quality. Lower quality waste generated from the washing line can be effectively repurposed for creating Recycled Polyester Staple Fiber (RPSF) through a finisher system that increases the intrinsic viscosity of the melt.
In conclusion, the Indian PET bottle recycling industry is undergoing substantial transformations, with a strong focus on fibre production and potential developments in RPOY/RFDY and B-to-B recycling. Addressing technical challenges and optimizing production processes will contribute to achieving higher quality recycled products.
(Santtossh Ughade is the author of this article, and he is the director of Santech Machinery And Equipment Pvt. Ltd.)