Sustainability Is The Key To The Trend In Textile Business
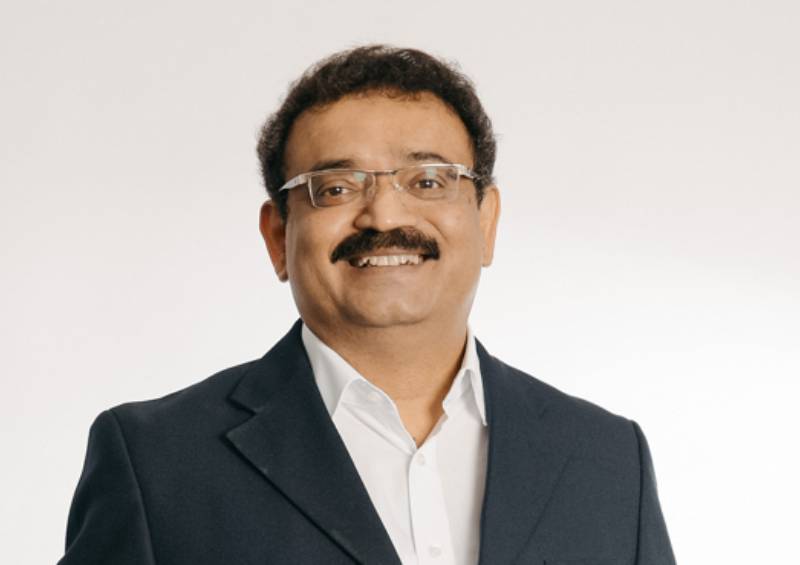
WEKO’s main target is to reduce the use of the resources, which results in potential reduction of emission/consumption and waste generation, says Jayanta Sanyal
How do WEKO’s products strike a balance between sustainability and cost savings in the textile manufacturing process?
WEKO’s revolutionary non-contact rotary atomiser spray application works on the principle of exact precise minimal application. The main targets are to reduce usage of water, reduce use of chemicals and their wastage, reduce drying energy, reduce material wastage and increase operational safety.
In textile value chain, each process consumes different resources resulting in emissions/consumption/waste generation. As stated earlier, WEKO’s main target is to reduce the use of the resources (water, chemicals, energy etc.), which results in potential reduction of emission/consumption and waste generation.
Depending on specific process of dyeing as well as finishing, the extent of saving is different. This can vary between 35% up to 80% in terms of different resources. So, focusing on sustainability directly helps the manufacturer to save the expenses of production and that’s the balance.
India is emerging as a key market. How does WEKO anticipate the demand for its products evolving in the Indian textile industry?
India is definitely emerging as a key market not only for sales but also for manufacturing. Government of India’s different initiatives clearly reflect this constructive aggressive intention. Make in India, SAMARTH, ATUFS, PM MITRA, PLI Schemes, National Technical Textile Missions, etc. are well-known now-a-days. Even though WEKO is active in various industry sectors since last 70 years, only in textile, nonwoven, technical textile industries we are anticipating a sharp increase in demand of WEKO and Rota Spray’s minimal application technology. We can clearly visualise the increase in the turnover in 2023 compared to previous three years and we have already had a number of serious discussions from different sectors of textile and nonwoven industries at the beginning of 2024.
WEKO is listed in Annex III of Indicative List of Machinery Manufacturers under ATUFS of Ministry of Textiles, Office of the Textile Commissioner, Mumbai, and the textile mills can take the benefit from this while investing in WEKO.
Are there specific challenges that WEKO’s products address to make Indian textile manufacturers more competitive?
In the textile supply chain, there are always challenges and these challenges are increasing manifold for the Indian market. The main challenge is the dramatic increase in textile fabric as well as garment manufacturing in different countries in S-E Asia. The increase in volume of manufacturing is therefore forcing the manufacturers to reduce sales price to sustain in the price competition. One dollar saved is one dollar earned. WEKO’s different products of fluid and powder applications are focusing on savings to help manufacturers to sustain in the more and more competitive market.
Considering the evolving landscape, what trends do you foresee in the textile industry, and how is WEKO adapting to these changes?
Sustainability is the key to the trend in textile business. While selecting the vendors, the brands and the retailers are focusing very deeply on the initiatives that the manufacturers have already adopted or are willing to adopt in their manufacturing processes to achieve the sustainability goal. It’s a process of continual improvement and adaptation of sustainable processes. Depending on specific process, WEKO is continuously adapting to develop, implement and provide specific solution which not only brings sustainability in processes with improvement of product quality and consistency as per the requirement of the brands and retailers, but also increase profitability of the manufacturer. As a German company, WEKO is continuously working together with universities, chemical companies, other machinery manufacturers, brands and retailers and also with the digital and print media of textiles to understand, develop and implement the most effective solutions.
As a result of that, our PS2 process is becoming more and more popular for cotton fabric dyeing with reactive and vat dyes where the manufacturers can successfully withdraw the huge drying unit in conventional PDPS process and can save almost 1400 tonnes of CO2 per machine per year.
Understanding these requirements, WEKO developed different processes as well as application systems like WEKO Sigma, WEKO ProTec, WEKO Neo and Rota Dyer Twin.
Are there new innovations or developments in WEKO’s pipeline that align with upcoming trends in the textile sector?
There are number of innovation and development projects in WEKO’s pipeline. We first develop the process and then we go for application developments.
There are two steps: 1) Technological study, 2) Lab tested and ready for market.
Presently, we are working on different projects, such as:
- Near infra-red (NIR) drying using renewable energy
- Polyester disperse continuous dyeing with Spray-Dry-Cure process which will save more than 80% of water and production time and lots of energy to run the conventional jet dyeing machines.
- Pad-Spray-Batch (PSB 35) instead of CPB to reduce batching time.
- Single side digital print preparation application to increase the speed of digital printing.
- Different other single side applications over high GSM textile or nonwoven materials required for specific end-use.