WTT Only Supplier Of Single Skid RO With 97% Water Recovery
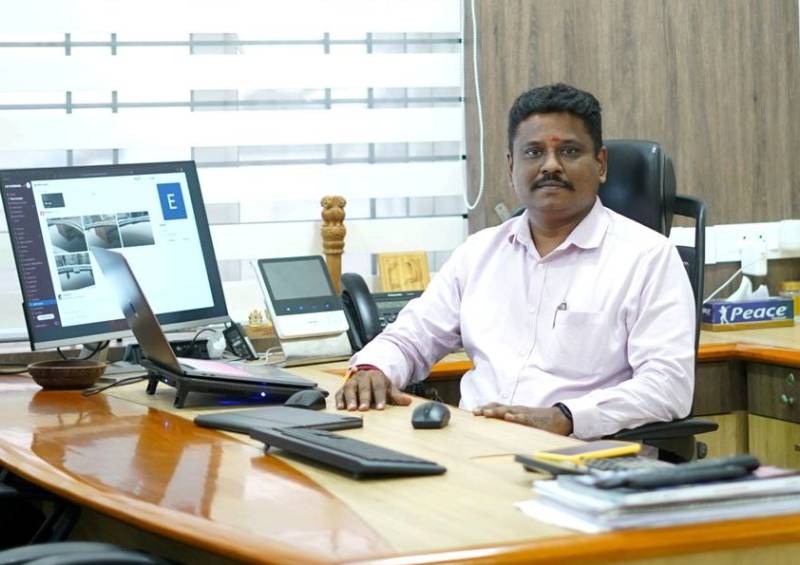
Tirupur headquartered WTT International, a pioneer in manufacturing Zero Liquid Discharge (ZLD) technology, has evolved as the only player, to provide highest water recovery of up to 97 percent, with a single skid Reverse Osmosis (RO), as against its competitors offering multiple skids of RO.
Due to the single skid RO, WTT customers are benefited from reduction of operating cost, chemical dosage and electricity consumption also decreases.
WTT also supplies the first of its kind Effluent Treatment Plants (ETP’s) with integration of IoT and so ETP’s supplied by WTT enable customers, to monitor the effluent treatment process by using the WTT Mobile Application.
Additionally, the plants are completely automated and involve very less manpower. WTT also supplies effluent treatment plants with lowest operational cost, high ease of operations, highly advanced technology integrated systems, while needing very less land space to set up the plant.
WTT International formerly known as WTT Technology Services is headed by D Venkatesh who started providing water treatment services in 2003 and commissioned its first ZLD plant in 2004, while also setting up its European office in Italy in 2018, and till date has commissioned more than 67 projects.
WTT has a world class manufacturing facility which can fabricate and manufacture almost 10 Effluent treatment projects which on total can treat a capacity of two crore liters every day, while having a very well equipped team of engineers from various domains, along with up-to-date software and tools.
The company manufactures water and waste water treatment solutions including and not limited to ZLD’s. These include Effluent Treatment Plants, Sewage Treatment Plants, Reverse Osmosis, Caustic Recovery, and Brine Recovery Systems.
WTT International is supplying these solutions to various industrial sectors like Textiles, Tanneries, Plastic Recycling, Refineries, Food and various other industries. WTT offers turnkey services in effluent treatment plant, technology up-gradation, operation and maintenance services.
“WTT has supplied its solutions in all the textile hubs of India including Tirupur, Bhilwara, Ludhiana, Bhudni, Mohali and Ahmedabad. Market leaders like JCT, Welspun, Vardhman, LNJ, Trident, Birla Century, etc are our satisfied customers,” WTT International MD, D Venkatesh told Textile Insights proudly.
“We even have customers who have given us six repeat projects continuously over a period of five years. WTT has now received an order from Bangladesh, which is a great start for our export journey and we also have an active agent network in Bangladesh, Iran, Uzbekistan, Mexico and Indonesia,” he added.
WTT International has three patented technologies to its credit which are CaRe, Rewolutte and Brinex. CaRe enables to recover clear caustic from the spent caustic and this system increases the number of times the caustic stream is getting recycled. The cost of adding huge amount of caustic will be reduced by this system thereby enabling customers to save on operating expense.
Rewolutte is an innovation in Reverse Osmosis technology by which 97 percent water recovery can be obtained in a single skid of RO. This technology reduces capital expense by 15-20 percent and increases ease of operation along with reducing operating expense.
Brinex is a technology to recover brine from the concentrate stream of Reverse Osmosis system and comprises of a sequence of processes. This system reduces the feed to the Evaporator and brings down the total operating cost. Brine which is recovered will be of 120-140 GPL and can be used to replace salt consumption in textile processing.
WTT is now investing in R&D capabilities and is in the process of setting up a highly advanced and fully equipped R&D Centre. It is also working towards developing its engineering and fabrication facility to supply minimum 25 ETP’s per year from 2025.
On his expectations on the future growth and opportunities in the Indian textile industry, D Venkatesh informed that ETP’s and ZLD’s are the need of the hour and that they are already seeing a tremendous change in the mindset of textile manufacturers towards treating effluents.
“We play a very major role for enabling sustainable growth to our customers. Various Pollution Control Boards and global garment buyers have started insisting that manufacturers go in for ZLD technologies as a part of their sustainability initiatives. Therefore we see a very positive and increasing demand for our technologies in the very near future,” he stated.