Arcus Printers Launches Instant Peel DTF Transfers For Faster Printing
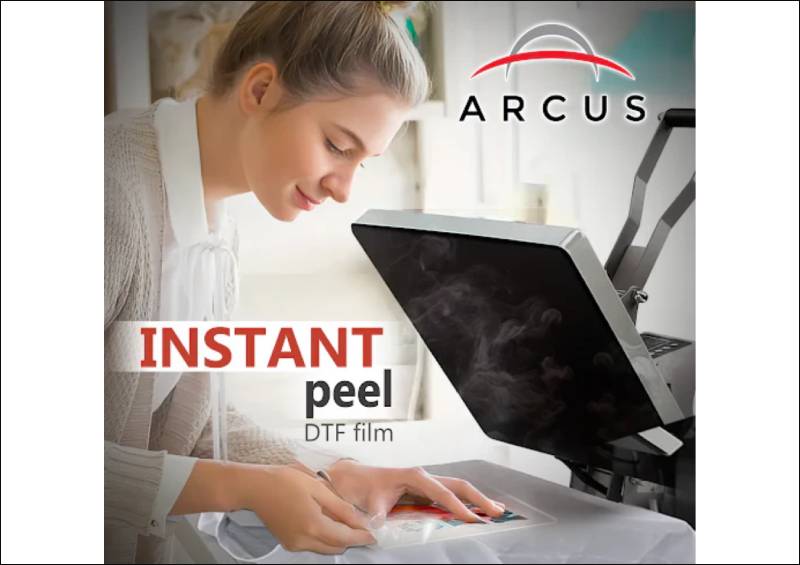
Arcus Printers launched its latest innovation, Instant Peel DTF Transfers. These state-of-the-art transfers are designed to tackle the common challenges faced by decorators using traditional cold and hot peel methods, offering a faster, more efficient and reliable solution for the transfer process.
Instant Peel DTF Transfers are engineered to revolutionize the application experience by combining the best features of cold and hot peel techniques while eliminating their drawbacks. With a rapid peeling time of just one to three seconds, these transfers significantly enhance production speed, making them ideal for high-volume orders and quick turnarounds.
Rick Marcelo, Director of Technology at Axiom America, the parent company of Arcus Printers, stated, “Our new Instant Peel DTF Transfers address the pain points decorators have faced with cold and hot peel methods. We’ve combined speed, quality and durability in a single product, allowing decorators to achieve faster production times without sacrificing design integrity.”
The key features of Instant Peel DTF Transfers include a fast-release mechanism, ensuring decorators can efficiently complete projects. Many users prefer the two-press method, where the first press liquefies the powder adhesive for proper adhesion, and the second press, often with a slip sheet, allows the ink to settle deeper into the fabric, resulting in a smoother and softer finish.
Additionally, these transfers deliver enhanced colour vibrancy and clarity that rival the best cold peel options, without the long wait times. Designed to withstand 35 to 40 washes, they meet industry standards for washability and durability. The advanced formula also provides superior abrasion resistance, ensuring that designs remain intact and vibrant over time.
Moreover, the Instant Peel DTF Transfers feature a unique double-sided anti-static coating, preventing buckling under the heat press and ensuring a clean peel every time. Unlike other fast peels that may compromise quality, these transfers solidify the adhesive immediately upon peeling, ensuring a strong bond with the garment and minimizing the risk of lifting or peeling.
In comparison, traditional cold and hot peel transfers each have their limitations. Cold peel transfers produce sharp, detailed prints but require cooling time before peeling, which can slow production. They are also susceptible to burning at high temperatures. Conversely, while hot peel transfers are quick to peel, they often lack colour vibrancy and can lift off the garment if not pressed correctly. If pressed too long, they may re-attach to the transfer paper, leading to inconsistent results. Additionally, their adhesive layers may not hold up after multiple washings and poor-quality films can struggle with ink absorption, causing fine details to peel.