Osthoff Offers Sustainable Technology For Producing Superior Quality Knits
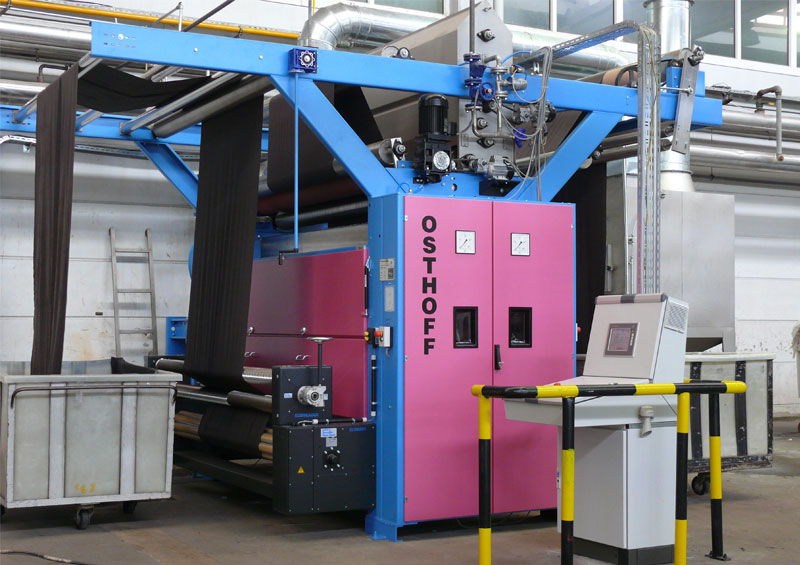
Bio polishing is a commonly used treatment for cleaning knit fabrics to improve their quality. However, there are many challenges inherent in this process:
- Fluff management on the shop floor
- Considerable reduction in depth of the shade after bio polishing
- No consistency in results, as it is a batch wise treatment
- High weight loss
- High tensile strength loss
- Expensive chemistry
- High increase in the COD volume and process effluent due to the water and auxiliaries used for bio polishing
- Bio polishing is additional process which increases effluent volume
Bio polishing hence has high costs associated with it. Moreover, with ecological concern and sustainability assuming global importance, it is even more important imperative for the industry to change its processes to address these concerns. Continuous open width singeing is an excellent, economical, and sustainable alternative that can effectively overcome the challenges posed by bio polishing.
A.T.E., the complete solution provider in textile machinery, represents Osthoff-Senge GmbH, Germany, the market leader in open width singeing technology. Osthoff-Senge has specially developed a new singeing machine for processing open width knit goods with working width of up to 2600 mm.
Open width knit singeing offers many significant advantages, such as:
- Improved surface quality
- Reduced loss of weight and tensile strength
- Lower production costs
- No increase in effluent loads
- Clean shopfloor
- Consistency in results
Features:
- Well proven double jet burners
- Proportional gas: air mixing and pre-selected singeing positions
- Selvedge uncurling, driven spreading scroll roll assembly and centering devices
- Short distance between the guiding rollers to prevent the selvedge from rolling off
- The fabric is protected by a water-cooled roller when the flame is active
- Designed to singe either on one side or on both sides of the fabric in one passage
- After the singeing, the material is guided to a suction cleaning unit
- On top of the singeing machine a fabric pull roller is installed to pull the fabric from the machine without any stretch
- To avoid any fire hazards, the knit fabric is guided via a scroll roller into a steam box
- Finally, the fabric is delivered via a plaiter into box carriages
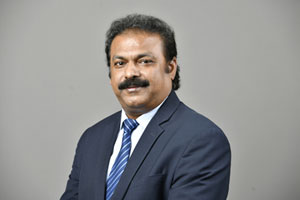
S Rajendran, Sr. VP, Business Head – Textile Engineering (Processing and Accessories) Zonal Head – South India
Around 150 Osthoff open width knit singeing machines are now working satisfactorily across the world. Three machines are already working in India: Tee Jay (Vishakhapatnam), Bhoomi Textiles (Ahmedabad), and Victus Dyeing (Tirupur).
Many delighted customers have acknowledged that the operational cost of the Osthoff knit singeing machine is nearly 50% lower than the bio polishing process.
A.T.E.: a perfect partner for you
A.T.E. has always been dedicated to offering the state-of-the-art, efficient, and eco-friendly equipment that help our customers gain a competitive advantage. The concepts of responsibility and technology are part of the values of A.T.E.
Apart from supplying a complete package of machinery for the processing industry, A.T.E. offers after sales services, technological support, AMCs, machine audits, etc. We have a rich experience of executing many green field projects.