There Is An Urgent Need To Create Sustainable Yarn To Address Global Warming
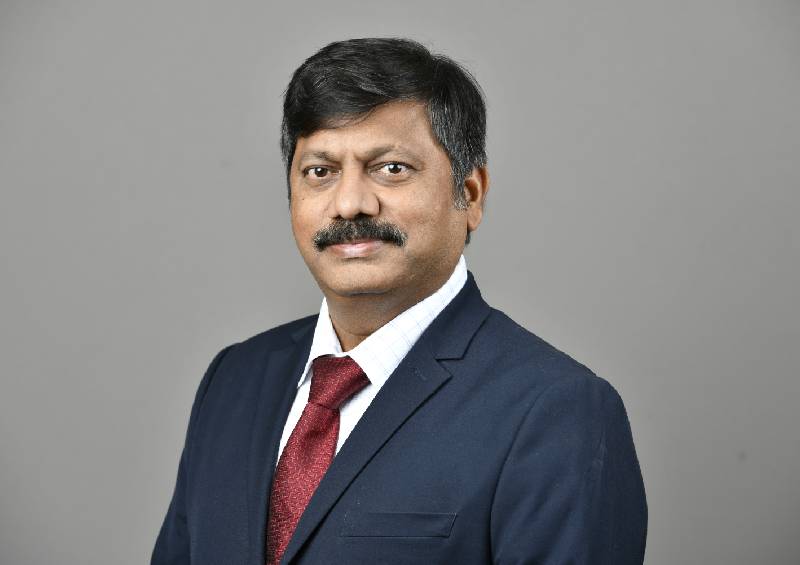
Indian textile spinning has modern machineries and very good work practices to produce good quality cost-effective high-quality yarn, says Kiran Hanchate, in conversation with Henry Dsouza, the Associate Editor of Textile Insights.
How has technology in the spinning industry evolved over two decades and what kind of impact did it have on productivity and quality?
Over the past 25 years, technology in the spinning industry has significantly improved productivity and quality. The latest generation machinery right from blowroom to winders are equipped with high technology engineering, demands less maintenance intervals and few breakdowns, AI for problem-solving and data base management, automation has led to high production with less HOK.
Better feeding and control system right from blowroom like the Trützschler advanced conti-feed system, the high precision servo drives, advanced sensor for auto levelling system in cards and draw frames, T-Go the Trützschler automatic cylinder to flat tops setting, the Magnatop in Trützschler cards, twin drive and piecing optimizers contribute to high quality sliver which helps to produce high quality and consistent yarn with higher production.
What are some of the common challenges faced by the spinning industry, particularly in recent times, and how is the industry addressing these challenges?
The spinning industry faces challenges like unpredictable yarn demand and higher yarn costs due to raw material price fluctuations. In recent times the US and Europe’s recession has impacted Indian yarn exports and the low yarn demand with high raw material cost has impacted the profitability of spinners. Import of synthetic fabrics at low cost from Bangladesh and China has impact domestic synthetic industry.
How does the selection and sourcing of cotton impact the spinning industry, considering factors like quality, count and market focus?
India is the second largest cotton growing country and spinners in India have wide varieties of cotton to choose, depending on count, yarn quality, mill location, machinery setup in their mill and the product position and quality and count to be produced.
Average data of last 10 years of cotton cultivations is 12.5 mn hectares with average output of 35 mn bales. But many things changed in the industry in the last 10 years. The spindleage, production, demand fluctuations, climate change, demand for other commercial crops, change in international cotton prices, circular economy, sustainability and recycled products in demand, garment product cycle and fashion changes do impact yarn price and are hence decisive factors for cotton sourcing.
How has the global cotton market affected the spinning and cotton industry in India, particularly concerning cost, innovation and market reach?
India’s yarn industry faces challenges due to a lack of integrated value changes with changes in fashion and demand globally. The dispersed textile industry with spinning, weaving and processing mills and cotton grown in different states leads to reduced efficiency with higher costs. We also lack FTA trade agreements with global purchasing countries and strong government polices to achieve higher market share in global trade. India must streamline its cotton to garment supply chain, leverage spinning expertise and establish robust garment manufacturing capabilities.
How are changing market trends, such as the demand for sustainable and eco-friendly products, influencing the cotton and spinning industries?
Sustainability is crucial in the textile industry to reduce landfill. More than the demand for sustainable yarn there is an urgent need to create sustainable yarn to address global warming. Handling post-consumer wastes like segregation of cotton, blends, garment accessories like hooks, button, zips, etc. demands high manpower and large space to handle. Apart from this, fibre generated from post-consumer waste are challenged to produce good quality yarn for spinners due to short fibres and limited length of fibres. While yarn buyer expects quality at par with virgin cotton, spinners have a huge challenge to meet the quality.
More organic cotton should be grown as it is very much sustainable, but its higher cost and lower yields need to be addressed.
Consumer awareness and education, particularly among the younger generation, will increase the demand for sustainable products. Collaboration among consumers, manufacturers and policy makers is needed for an eco-friendly textile sector.
Considering the factors of technology advancement, market shifts and substantial requirements, how do you envision the future of the textile spinning and cotton industry?
The Indian textile spinning has modern machineries and very good work practices to produce good quality cost-effective high-quality yarn. Currently, Indian yarn has share of 35% in global yarn market, while it is less than 5% in global clothing. Finally, its the garments that are consumed by customers. Apart from current yarn exports, India should increase the share in global clothing to increase the demand for yarn further. Cotton is India’s strength and should be leveraged from yarn to garments.
Could you please elaborate on A.T.E Group’s commitment to sustainability and its various initiatives within the textile industry?
A.T.E Group has always been a textile industry pioneer in embracing technological advancements and promoting sustainability across various dimensions. Trützschler Group has partnered with Balkan Textile Machinery, specialising in fabric opening and cutting machinery for recycling, to offer customers additional sustainability solutions.
A.T.E is committed to sustainability in the textile supply chain from fibre to garment, and it actively explores sustainable practices in fabric forming and processing. Our dedicated ETP division focuses on zero-discharge water treatment, emphasizing sustainable water management. We promote solar energy systems as part of our sustainability efforts, offering solutions that not only harness renewable energy but also reduce carbon footprints.
We offer IoT systems that provide utility data to customers, enabling them to control their utilities more efficiently and reduce power consumption, thus contributing to sustainability goals. Our HMX division specializes in comfort cooling, utilising fresh air to enhance comfort and promote sustainable practices within departments. In principle, A.T.E Group is dedicated to sustainability in the textile industry, focusing on air quality, water management, renewable energy, IoT-enabled utility control and innovative cooling solutions.