Uster Tech’s Sustainability Bulletin: Navigating Recycled Textile Challenges
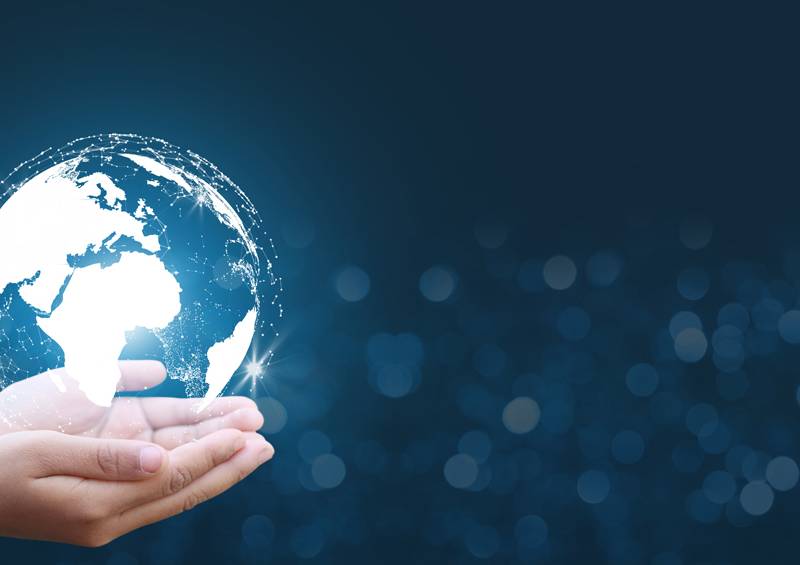
Uster Technologies comprehensively addresses the narrative of recycled textile materials in its application report, Sustainability Bulletin No. 1. This publication underscores Uster’s dedication to supporting the use of recycled materials throughout the entire textile value chain.
Many contemporary consumers already anticipate the incorporation of recycled materials in the clothing and home textiles they purchase. This expectation is a driving force behind innovation in the industry. However, there exists a level of uncertainty regarding the implications of this trend for yarn producers, both economically and technically. The inaugural Uster Sustainability Bulletin outlines the challenges and proposes solutions.
Starting Positions and Results
In textile processing, spinners are frequently tasked with producing yarns using recycled materials while maintaining comparable quality to those from new fibers. Gabriela Peters, Head of Product Management Laboratory Systems at Uster Technologies and one of the authors of the bulletin, notes, “The use of mechanically recycled fibers in spinning involves specific quality considerations. Such fibers often have a higher short-fiber and nep content and may be colored, especially when post-consumer material is used.” Additionally, recycled yarns have limitations in terms of yarn fineness. Thermo-mechanically and chemically recycled fibers and filaments are anticipated to pose fewer processing challenges, exhibiting similar processing behavior to new fibers and filaments from synthetic and viscose materials.
The Sustainability Bulletin focuses on addressing the challenges associated with more problematic recycled raw materials. For instance, it delves into potential difficulties in various process steps in spinning, aiming to bring clarity and understanding about mechanically recycled materials and offering ideas on how to process them.
Studies indicate that yarns and fabrics produced from recycled fibers may be better suited for applications where the strength of yarns and fabric is less critical but where control of unevenness, imperfections, and handle properties is crucial. Consequently, recycled fibers are most suitable for manufacturing casual clothing items such as T-shirts, sweatshirts, and sleepwear. In China, tons of denim jeans trousers are already made from mechanically recycled fibers.
The Guardian of Quality
Uster Technologies sees its role as a knowledge provider, establishing definitions and standards to expedite the ongoing transformation of the industry. As a long-term trusted supplier of quality control systems to the textile manufacturing industry, Uster assists the industry by evaluating test results, guiding spinners on the current possibilities for dealing with recycled material in its various forms.
The Uster Statistics benchmarks are invaluable for measuring, controlling, and improving quality. The new edition, launched at ITMA 2023, includes a section for recycled yarn for the first time. The Uster Statistics 2023 edition also features an extended range of fiber data, supporting sustainability goals. It is a fact that an ideal fiber mix, with or without recycled content, must also meet quality requirements to minimize waste.
Uster understands its function as a neutral arbiter, reporting what quality can be expected when processing different recycled materials. Uster’s expertise on using recycled raw material is compiled in Sustainability Bulletin No. 1 and is available for free download at www.uster.com/sustainabilitybulletin
Cooperation for a Sustainable Future
Effectively and efficiently using recycled materials will be key to success in future years. To achieve acceptable results and profitability, all segments of the textile chain must cooperate and learn from each other to avoid collective failure. “At Uster Technologies, we firmly believe it’s a great opportunity for textile manufacturers to lead this momentous industry transformation, as recycled fibers are the raw material of a sustainable future to be processed into new products,” says Peters.