Innovation Versus Tradition – The Power Of Defying Convention To Produce Blended Yarns
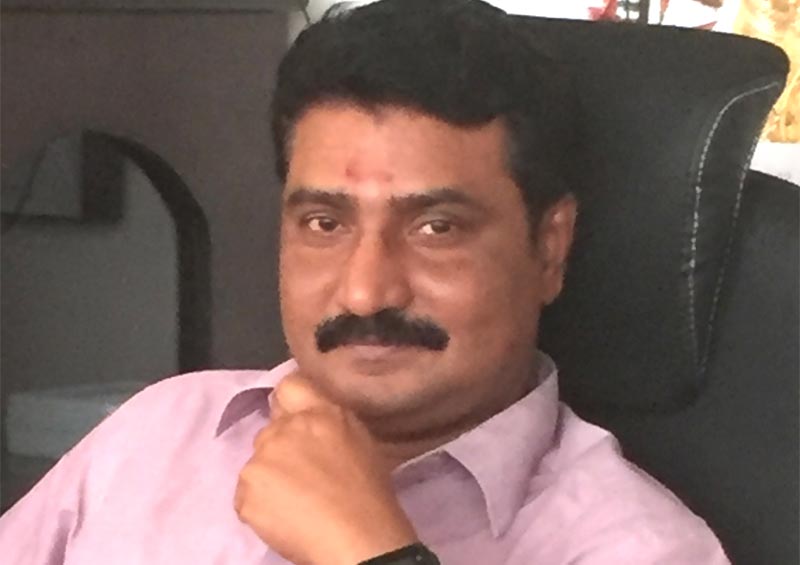
The air in the spinning mill, usually alive with the rhythmic hum of machinery, seemed suddenly crackled with tension.
The centralised QAD in-charge for our group of textiles stormed into my room. His eyebrows seemed perpetually furrowed like a disapproving schoolmaster. His voice was more like a throaty growl, as if to convey some frustration as well. He almost barked at me. “What you’re doing is violation! Synthetic fibres through combers? Never done, never recommended!”
I tried to keep myself cool, and voluntarily brought a smile on my lips. “Relax, sir!” I soothed, gesturing to a chair. “Tell me what’s got you in such a twist. We’re all here to solve problems, remember?”
Neither my words nor the cold air from the AC seemed to cool him off. His face remained red like a beetroot. He lashed at me. “In my decades in textiles, I’ve never heard of such contradictory process! Blending synthetics at combers? Madness!”
“But sir,” I countered, my voice calm but firm, “our customers love the yarn. They pay a premium for its quality, its softness, its uniformness in blending and less IPI.”
He slammed his fist on the table, rattling empty coffee mugs. “I cannot tolerate any action that goes against our established norms! I’m reporting you to the management!”, he growled.
A flicker of steel entered my eyes. “Do it!” I challenged. “If that’s your decision, let them hear us both.”
He huffed and his bluster deflated by my unwavering resolve. With a final glare, he stomped out, leaving me in the stunned silence of the room.
Then, the long story short, he reported to the management, and to his disappointment, the management replied the same as I told him.
The Story Behind This Incident
This incident happened some 15 years back. We had been supplying yarns from SUVIN, known for its silken touch, to a renowned Japanese lingerie brand, a brand always pushing the boundaries of comfort and sustainability. For sustainability and to improve the quality related to softness and moisture management, the brand intended to blend micro Modal and Tencel with Suvin.
We tried the following two traditional methods of blending.
- Blending at blow room, in which combed slivers of cotton and virgin fibres of Modal/Tencel are mixed at the required ratio and then processed through the carding process.
- Blending at the draw frame, where cotton and Modal slivers are processed separately from blow room to drawing, with cotton combed and Modal carded.
We supplied samples of yarn from both the above methods of blending. Each had its flaws, like an off keynote in a melody. The verdict from our customer favoured blow room blending for its thorough and uniform blend level, but criticized its imperfections. In contrast, draw frame blending yielded good IPI results, but lacked in uniformity in blending.
Innovation in Blending
At that point we realised that we needed a new verse, a revolutionary riff.
Through many internal meetings, we came up with the idea of blending these fibres at the sliver lap machine. We processed the Modal fibres at the blow room with minimal beating points only to open them gently. The card settings were opened to avoid damaging the fibres. We had less combined process waste at these machineries, after reusing some of the process waste.
Previously we had checked the noil percentage for 100% modal, which was around 4%, whereas 100% cotton had a noil percentage of around 18%.
Factoring in waste percentages, we calibrated the hanks of the carded slivers of both cotton and modal to achieve the desired blend ratio at the combed slivers. While producing yarn samples from this method, we also checked the blend ratio in a renowned research institute and confirmed that it was within the standard level.
The yarn from this method was approved by our customer, and with additional special filaments, they produced inner garments for winter under name of “Hot Cotton” that set sales records ablaze.
Parting Thoughts
This was a testament to the power of defying convention. It was a yarn spun from our willingness in taking bold steps to challenge the status quo and write our own textile odyssey.
Though many years have passed, I overheard that the blending method has still been followed for that customer. And today, as the world embraces sustainability, where it has become imperative to blend different kinds of sustainable fibres along with cotton, this method may be useful to cut short the tedious blending process at the blow room and, at the same time, maintain the uniform blending quality as done at blow room with better IPI level. With this method, we may save energy and labour to achieve a sustainable production.
So, the next time we face a challenging situation, let us defy the ordinary and traditional ways and dare to rewrite the new rules.
(Murugan Santhanam is the author of this article)